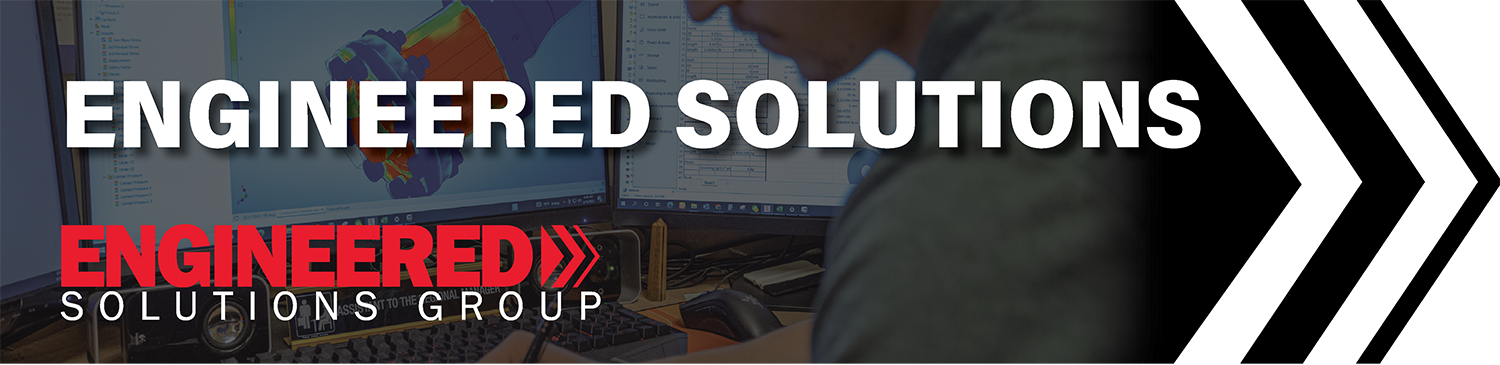
Case Study: Parker Hydraulic Actuator System (HAS)
The Problem:
A MCE customer was having an issue with plastic cap dumping machines used in an automated system. This customer was utilizing a ball screw (electro-mechanical) which had failed prematurely. The premature failures were creating unexpected costs and downtime, so the company called in MCE to provide a solution.
The Solution:
The MCE team--made up of Outside Sales Representative Jeff Blankiewicz and Technical Sales Engineer Aaron Stewart--first considered a traditional hydraulic power unit along with a cylinder to complete the job. But Jeff had a better idea. He suggested using a Hybrid Actuation System (HAS) unit—what he felt would be a smaller and simpler solution. By varying the speed of the electric motor, the customer would be able to control the velocity of the cylinder rod which equates to how fast or slow the plastic caps would be dumped out of the container. Due to space constraints in the automated positioning, the MCE team ordered the unit with the hydraulic power unit detached from the cylinder. The customer was able to input motion profiles in their PLC and use the linear transducer provided with the HAS unit to do this accurately. The HAS unit was a perfect fit.
The Value:
In addition to eliminating the additional costs and downtime caused by the premature failures of the ball screw, the MCE team's solution also provided the customer with a more energy-efficient solution because the HAS electric motor is designed to only use energy when needed.
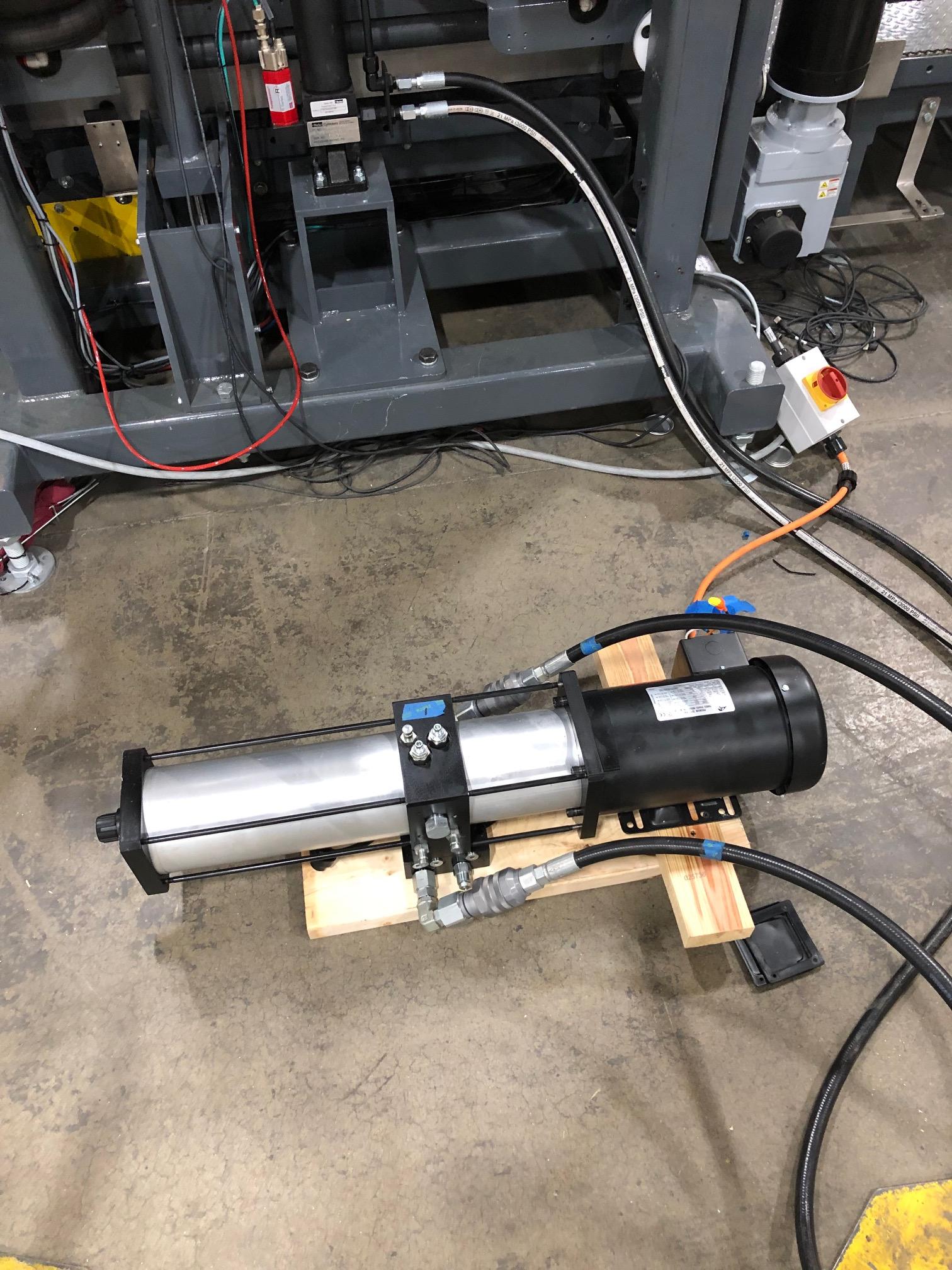
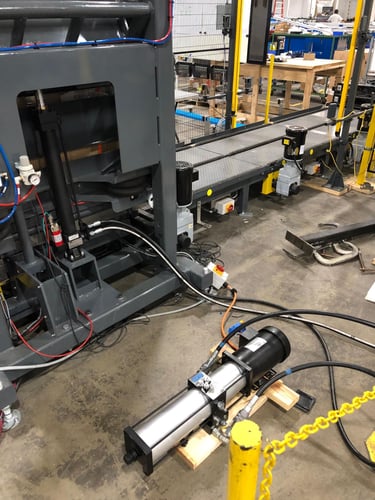
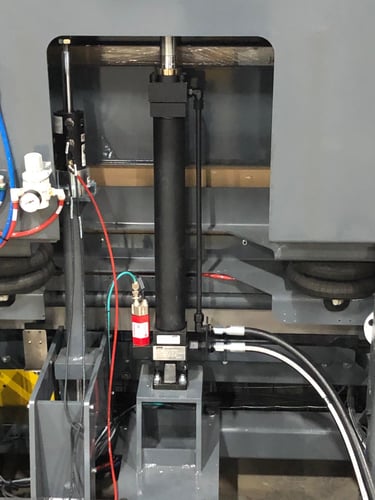
Detached hydraulic power unit
Detached hydraulic power, interconnecting hoses, and hydraulic cylinder with MTS position feedback.
Hydraulic cylinder with MTS position feedback
The HAS Actuator Advantage
- Low-Cost, Simplified Design removes the need for connected hoses and tubes because the entire hydraulic system is consolidated into a single component integral to the actuator
- 3x Power Density of comparably sized electromechanical solution because fluid transmission moves the actuator rather than a rotary screw
- 27% less wasted energy compared to traditional hydraulic systems due to elimination of the directional and flow control valving and locating the pump on the actuator
- Maintenance-free operation of over 8,000 hours with no need for hydraulic fluid change
- Plug and play control package for both industrial and control applications
Want to learn more?
Please click the button to the right and fill out an interest form so we can set up a quick call to discuss your specific application needs.